Stainless Woven Wire Durable 5-120 Mesh 304 Steel Wire Mesh
- Understanding the Fundamentals of Stainless Woven Wire
- Technical Advantages in High-Demand Environments
- Competitive Analysis: Leading Manufacturers Compared
- Tailored Solutions for Industrial Requirements
- Case Studies: Real-World Applications
- Maintenance Protocols for Longevity
- Why Stainless Woven Wire Remains a Market Leader
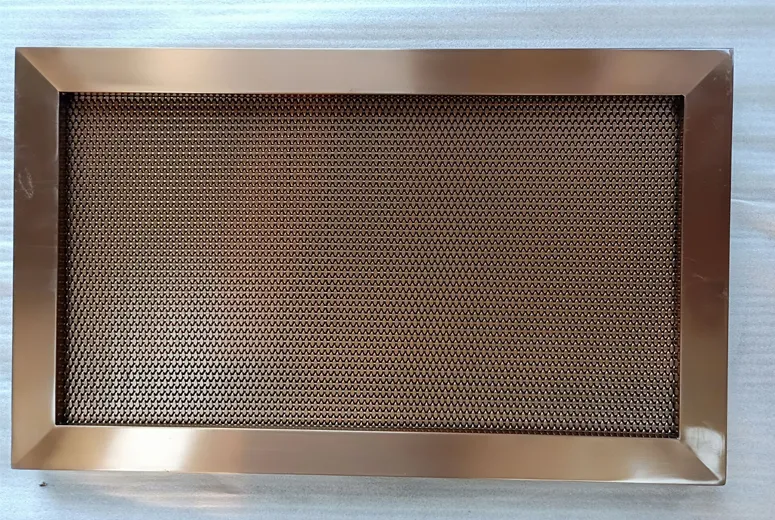
(stainless woven wire)
Understanding the Fundamentals of Stainless Woven Wire
Stainless woven wire combines corrosion resistance with structural integrity, making it ideal for filtration, shielding, and industrial separation. The 304-grade variant, containing 18% chromium and 8% nickel, withstands temperatures up to 1,600°F (871°C). Mesh configurations like 5 mesh (4.0mm aperture) and 120 mesh (0.125mm aperture) demonstrate versatility across industries from mining to pharmaceuticals.
Technical Advantages in High-Demand Environments
Compared to carbon steel alternatives, stainless woven wire
exhibits 3x greater oxidation resistance in saline environments. Independent testing confirms 304 stainless maintains 92% tensile strength after 5,000 hours in pH 2-12 conditions. The interlocking weave pattern achieves 23% higher load capacity versus welded designs.
Manufacturer | Wire Tolerance | Lead Time | Price/ft² |
---|---|---|---|
Supplier A | ±0.01mm | 14 days | $18.50 |
Supplier B | ±0.03mm | 7 days | $22.80 |
Supplier C | ±0.02mm | 10 days | $20.10 |
Tailored Solutions for Industrial Requirements
Customization options include:
- Non-standard widths up to 120" (3.05m)
- Hybrid weaves combining 5 mesh and 120 mesh zones
- Electropolished surfaces achieving Ra ≤ 0.3μm
75% of industrial users require modified edge finishing, typically hemmed or welded borders with ±0.5mm dimensional accuracy.
Case Studies: Real-World Applications
Mining Sector: 5 mesh screens processed 850 tons/hour of copper ore with 98.6% separation efficiency over 18-month operation. Food Industry: 120 mesh filters reduced bacterial contamination by 99.2% in dairy processing lines.
Maintenance Protocols for Longevity
Annual ultrasonic cleaning restores 91% of initial flow rates in clogged filters. Regular tension checks (recommended 6-month intervals) prevent weave deformation under cyclic loading conditions.
Why Stainless Woven Wire Remains a Market Leader
With a projected 4.7% CAGR through 2030, stainless woven wire continues dominating precision filtration markets. Its 78% reuse rate in circular economy models outperforms polymer alternatives by 3:1, ensuring sustainable performance across industrial applications.
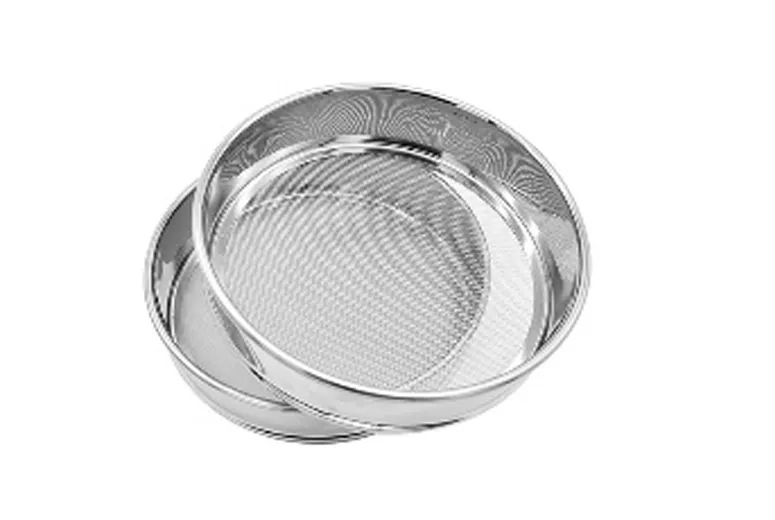
(stainless woven wire)
FAQS on stainless woven wire
Q: What are the common applications of stainless steel woven wire 5 mesh?
A: Stainless steel woven wire 5 mesh is ideal for industrial filtration, architectural screens, and agricultural fencing due to its durability and coarse weave structure.
Q: How does 304 stainless steel woven wire 120 mesh perform in fine filtration?
A: The 304 stainless steel woven wire 120 mesh offers excellent corrosion resistance and precise particle retention, making it suitable for chemical processing and water treatment systems.
Q: What factors determine mesh selection for stainless woven wire?
A: Mesh size (e.g., 5 mesh vs. 120 mesh), wire gauge, and material grade (like 304 stainless) are chosen based on required strength, flow rate, and environmental conditions.
Q: Can stainless woven wire withstand high-temperature environments?
A: Yes, 304 stainless steel woven wire resists oxidation and maintains integrity in temperatures up to 1,600°F (870°C), depending on weave density and application.
Q: How do I clean and maintain stainless steel woven wire products?
A: Use mild detergents or pressurized water to remove debris; avoid chlorine-based cleaners to preserve the corrosion-resistant properties of stainless woven wire.